My Store
Custom Plug-and-Play CNC Control Electronics System
Custom Plug-and-Play CNC Control Electronics System
Couldn't load pickup availability
Discover great performance with our Plug-and-Play CNC Control System, perfect for any CNC machine or router. Experience effortless plug-and-play installation and high-torque precision up to 12Nm with our ready-to-use solution.
Dominate the realm of CNC machining with our Plug and Play CNC Control System, intuitively designed for both might and precision, accommodating high-torque NEMA 34 motors up to 12Nm. Seamlessly integrating into your workflow, this system effortlessly elevates your craftsmanship to new heights.
Nestled within a robust cabinet, the system offers a complete solution with high-grade stepper motors, reliable drivers, solid power supplies, a power push-button contactor, and dual proximity switches for accurate axis calibration. For your peace of mind, an emergency stop button is conveniently installed on the cabinet to ensure you can halt operations instantly when necessary.
To maintain the integrity of your control signals, we provide shielded motor cables, sensor cables, and internal wiring to protect against any electrical interference.
Understanding the Base Price: At the core of our customizable CNC Control System are two base price options to cater to different needs. The first base price provides the essentials for those who are supplying only the CNC electronic components, covering expert labor for wiring, shielding, connectors, and the standard suite of cables for a 4x8 CNC machine, along with the robust cabinet and precision hardware for mounting. The second base price is for those who require a larger cabinet capable of housing a spindle VFD. If you have a VFD or wish to include one in your setup, you should select this base price option to ensure a perfect fit within your cabinet. Both options lay the groundwork for the additional components and features you'll select to complete your system.
Price Options and Customization: Tailoring your CNC system is straightforward with our transparent price options. Every selection includes high-quality power supplies, drivers, motors, CNC controller, and a contactor for the illuminated on/off push button—ensuring a cohesive and responsive setup. If you're not providing your own CNC electronic components, you'll need to choose between a 3-axis or 4-axis system, depending on the complexity of your projects. Additionally, select the size of the motors to match the power requirements of your operations. These choices will build upon the base price to form a complete package that's ready to perform right out of the box, catering to your specific machining demands. Specifications: NEMA 23 motors have a dual 1/4" (6.35mm) shaft (Dual shaft means there is a shaft at the front and a shaft at the back), NEMA 34 motors have a single 14mm shaft. The electronics will include the appropriate number of power supplies to drive all motors at their full torque along the full rated PRM of the motor (for example, a 4 axis NEMA 23 electronics requires 3 amps per motor which sums to 12 amps, so two 48V power supplies with 8 amps each will be included). The Mach3 USB controller is supplied with the standard electronics packages. If you wish to use Mach4, upgrade to the ethernet/usb controller.
Shipping Your System: Please note, the shipping cost is not included in the base price due to the custom nature of each system, which determines the size and weight of the final product. Shipping within the US domestic region is estimated at approximately 400 USD for freight. You may choose to arrange your own shipping method, or we can facilitate this for you, ensuring your system arrives safely and ready for integration.
With each purchase, ample cable is included for a 4x8 CNC router. Should your aspirations grow, additional cable is just a click away.
Our control systems are customized for your specific needs, and we ask for a two-week lead time to ensure you receive a product that meets our stringent quality standards.
For those setting up their system for Mach3, a Mach3 license will be required, conveniently available here. Mach4 enthusiasts are not left out—a Mach4 license is just a click away.
Choosing the spindle VFD upgrade not only broadens your system's capabilities but also adjusts the cabinet size to accommodate the additional hardware, with the pricing reflecting this enhancement. The spindle VFD is pre-wired for direct control, making it simple to manage your spindle's start, stop, and speed.
A Windows-based computer will bring this CNC control system to life, offering a stable and user-friendly platform.
Elevate your CNC experience with our Plug and Play CNC Control System, where safety and precision go hand in hand. Embrace fewer interruptions and more productive hours, whether you're carving intricate designs or charting the next course for your sailing ventures.
Explore Our Craftsmanship: We believe in showing you the precision and care that goes into each of our CNC Control Systems. To truly appreciate the quality and functionality of our work, we invite you to watch a series of videos showcasing our team assembling these systems and demonstrating what you can expect from your own. Witness the seamless process and the exceptional results that our systems deliver.
Share





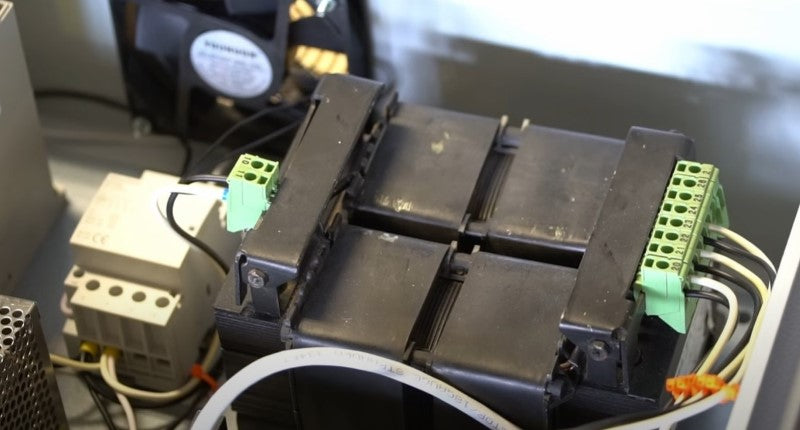

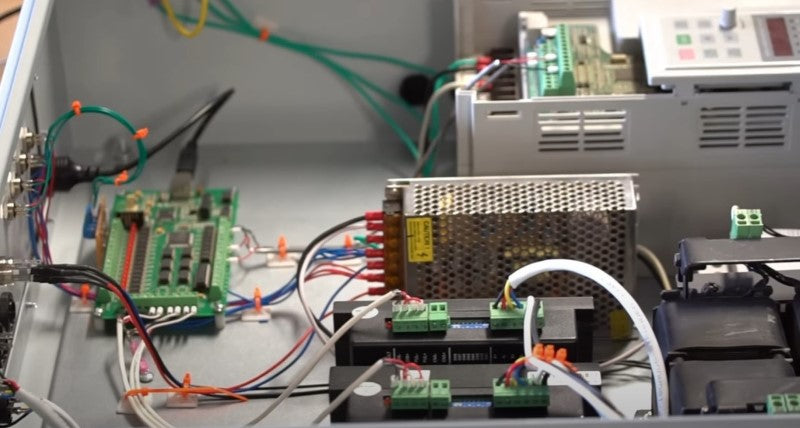


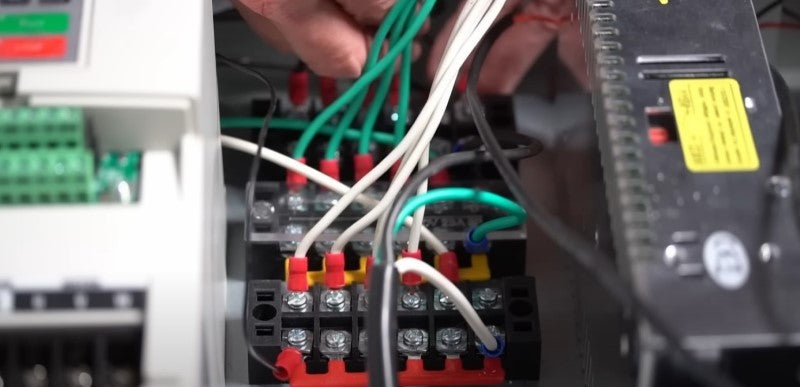

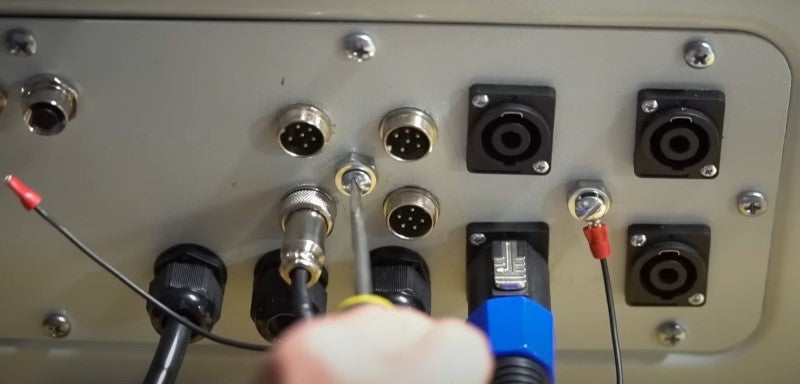



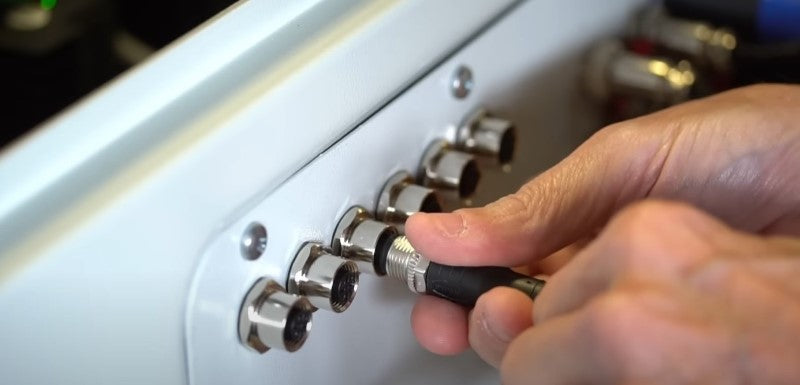

Questions & Answers
Have a Question?
-
I own a custom rug shop where we design a fabricate custom floors of many types, Have you performed any type of testing using your 40 watt and or 80 watt laser for the cutting of thse textiles.
Yes, we have cut many fabrics with the laser. Or CO2 lasers can generally cut fabrics and textiles without a problem. What types of textiles (materials) do you need to use with the laser machine? Is there a layering of materials? Additional Information: We would cut multiple heights of different carpets and even hard surfaces such as Vinyl composition tile, Luxury vinyl tile,etc. and I'm wanting to explore etching into plain color carpets using the laser. I'm contemplating your 5' x 12' machine with the laser/spindle combo. Is it possible to make a site visit to your location and see the capabilities of the equipment ? Additional Information: Carpets are not a problem as long as there are no materials in the carpet or in the carpet binding layers that will off-gas toxic fumes. Check the manufacturer's materials of all of the parts of the carpet. The vinyl should not be a problem, just make sure there is no material mixed within the composite that will off-gas harmful fumes such as chloride. The chloride will mix with the hydrogen in the air and form HCL (hydrochloric acid) which can be harmful if inhaled, but can also affect some of the metallic parts in the machine. We have cut vinyl with the laser with great results.
-
I have your nema 24 motors using the 36v power supply. Should I use the Bipolar series for the wiring the motors since I am using the 36 volt ad not a 24v power supply?
When connecting our power supply, no matter if it is 24 or 36 volts with our drivers/motors, you should always use bipolar parallel. This will allow you to have the best torque at higher speeds.
-
I have installed PCI card parallel port and all pins read 3.5v no matter which jog key is pressed can you suggest a solution?
If you are using a Parallel port card plugged into the motherboard in a PCI slot, or other compatible slot that interfaces directly to the microprocessor, you will need to make sure that the correct I/O address is entered into the configuration for your control software. This I/O address is the first one in the range that Windows, or other operating system, will provide when accessing that information. In Windows, you would need to access this information in the device manager. Select the LPT port that is associated with the added parallel card. The port address will need to be in hex form, not decimal. Other technical information that may help to understand the process: The operating system will provide the address range, the first will be associated with pin 1, and the remaining addresses in the range will associate to the remaining pins (excluding the gnd pins) of the parallel port. This provides high and low signaling for each pin when a one is applied to the address. This is the reason the parallel port is called parallel, since each pin is independent and can output, or receive input simultaneously.
-
I bought the book that you co-authored (Build Your own CNC) a few years ago. Its not till now that I�ll be able to start the project. Are all the parts still available? The book is about 8 years old now so I�m wondering if its still worth building that design? (I don�t see a newer version of the book)
This book offers an excellent platform upon which to learn CNC technology and fabrication no matter how old the book is. If you are new to CNC routers, I wuld highly recommend this book. The book will provide you with the plans and the knowledge to build a capable entry level CNC router and you will learn the fundamentals necessary to become successful with fabrication, maintaining the machine (and almost any machine), and how these complex CNC routers work. The machine kits on this website were created as an upgrade or alternative to the book CNC router build. Specifically the blackToe CNC Router: https://www.buildyourcnc.com/item/cnc-machine-blacktoe-v4-2x4
-
I bought a Blacktoe 2 x 8 three years ago and have always had a problem with the Zid axis. No matter how tightly I've calibrated the axis it always cuts to deep. Can I put a larger Stepper motor on Z-axis using the same motion electronics that came with the original machine.
Modifying the Z-axis to accommodate a larger motor will be a worth while task and is possible, however we have not calibrated the z-axis therefore using the 1600 Steps-per inch in the motor tuning on our machine in our shop. We have not noticed any significant depth increments from not calibrating the z-axis but only from zeroing the z axis too close to the material. Also in your design did you specify the actual depth and the length of tool (end mill/ bit) that you are using?