BuildYourCNC
Coupling Hub - 1/2" Bore
Coupling Hub - 1/2" Bore
Couldn't load pickup availability
This hub is typical used to fasten to a 1/2" lead screw. Note: To create a complete coupling set, you will need two hubs (one for the motor shaft and one for the lead screw end) and you will need one spider. These items are only offered to allow for any configurations that is not offered for rigid couplings.
Share
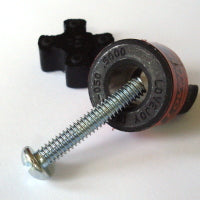
Questions & Answers
Have a Question?
-
would like to install 50k.potentiometer (2.45)to the back of my temp. gauge to set correct reading. will this work?
Could you please clarify the specific application and the desired outcome?
-
Looking for electronics for a plasmacam table. It's going to to be a 5'x10' table with x,y,z axis. Will be running on windows ten with a hypertherm powermax45 xp plasma cutter. Any information or links would be greatly appreciated!
What electronics do you have at the moment? Depending on your machine, you will need a minimum of 3 stepper motors and 3 drivers (unless your heavy axis requires two stepper motors and two drivers). You will also need an interface board that is capable of providing three inputs for the THC (Torch Height Controller), THC on, THC up and THC down, and outputs for firing the torch. I would recommend the Pokeys57CNC interface for the primary interface. This interface will connect to the stepper motor drivers and the THC. The Pokeys57CNC can also communicate via USB or Ethernet.
-
interest i nbuilding a 2X2' low budget 4-5 axes machine of 1-2 hp with tilting, rotating spindle up to 45 degrees off vertical
If you go to our R&D section, you can vote for your machine and/or type a special request to create a machine that you might need. R&D:https://www.buildyourcnc.com/ResDev.aspx
-
I have USB Interface board. All axes are working if using MDI , using program some of the axes are only moving one direction. Example using Gcode X50 Y50 Z50 and then X45 Y45 Z45 then online one of the axes is turning correctly. But also shows on Mach3 screen that all axes are moving correctly.
If some axes are not moving in two directions, the direction signal is not making good contact at either the controller or the driver.
-
I have a 4' X 8' table with carriages that use nema 23 motors. I have a hypertherm 45 plasma cutter. I have 20 degree 20 pitch rack gear. Can you suggest a plug and run system that I can use for cnc plasma and cnc routing?
Are you looking for replacement motors?
-
I have a 25 watt Epilog Summit Model 2000/25 laser engraver. I believe my tube is going bad due to limited vector cutting and no raster. Do you think there is a way to retrofit with your products to make it work well. Mirrors are new and mechanical is good. Thanks.
The laser tube is a consumable item in all CO2 lasers, unless the laser tube can be recharged. My laser tubes will most likely work as long as the mouts are the same size. Let me know the mount diameter and the length of space for the tube in the Epilog Laser Cutter and Engraver and I will let you know. Additional Information: My Epilog Summit (3.3) only works from Windows Millenium and 98. Notconsistently from WXP, but sporadic raster and vector combined does happen. I can't get it to work right w XP through Harvard Draw, Corel,Image Folio, Stika, DrawMagic or anything else I have. But Millenium isOK except for the advanced mapping to colors function is very difficult.When it does rarely accept a graphic from my XP system from CorelDrawEssentials or 8.0, it will allow complete control for photo etching -speed, power and shade mapping. It is the same driver for both mysystems but the control panel page looks different in the 2 computers. The laser takes 45 seconds to initialize after power on. You can use a USB to Parallel adapter cable for your laptop or modern computer connection. The laser needs the old style printer connection. Test your laser by holding all 3 power/focus/speed buttons until homed. Close the lid. "Online" for lase, any other button for laser off. Should be an audible beep every few seconds while your laser is functioning. This is not a motion test -only laser firing.